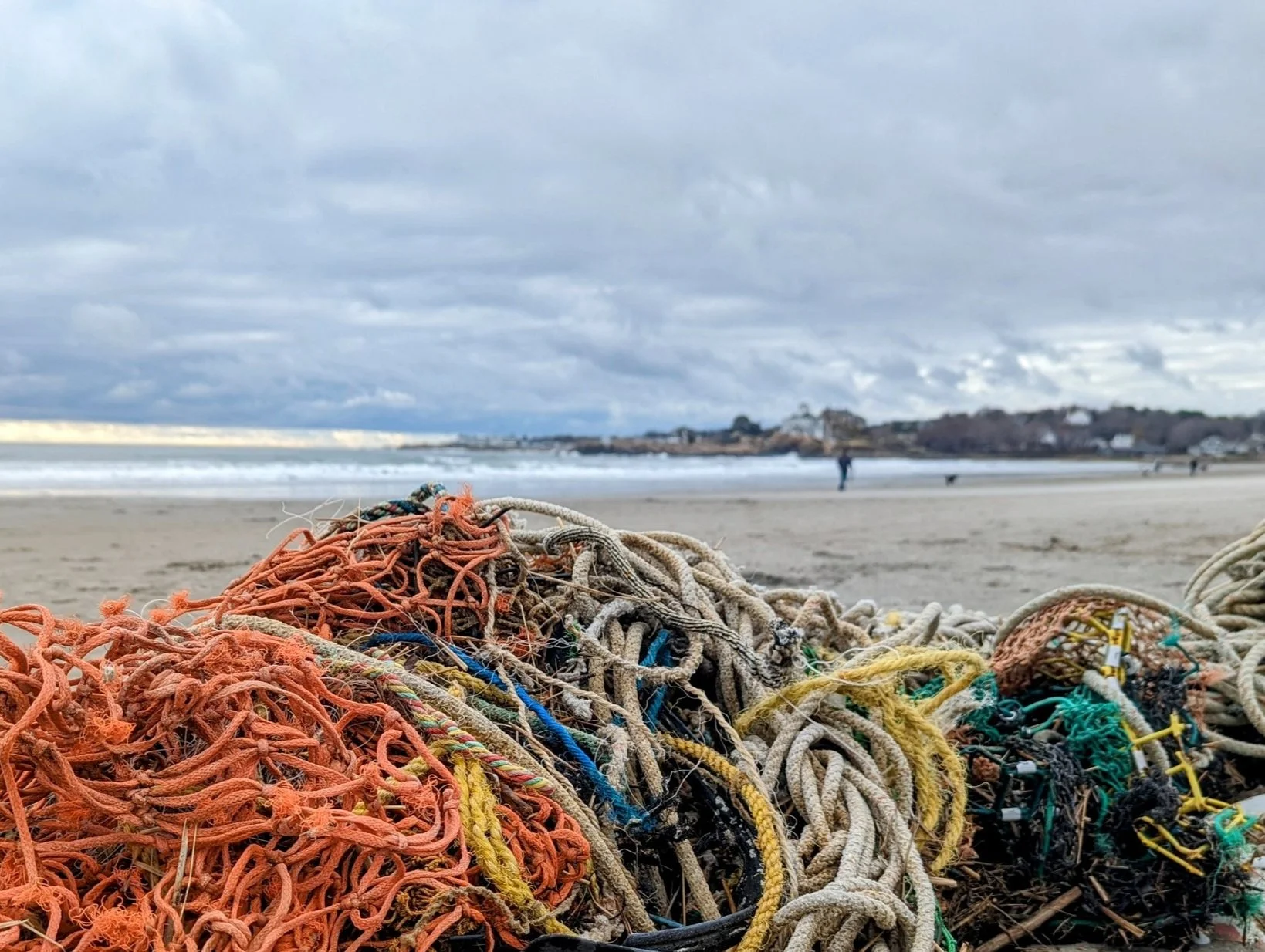
The world has plenty of plastic,
let’s use what we have.
Sustainability isn’t a business strategy, it’s a series of choices.
-
Recycled Plastic Core
We make lots of jokes about recycling plastic trash so we can put it in the ocean. But we wouldn’t be making surfboards if we had to use foam. The traditional shaping process produces a lot of fine foam dust, and we figure that there’s no way it stays out of the environment.
We also wouldn’t be using 3D printing if we couldn’t make durable boards with recycled plastic. Each of our boards keeps about 2 kg of plastics, the equivalent of 50 soda bottles, out of landfill. More importantly, our surfboards are built durable enough to sequester that plastic waste for the next few decades.
-
Low Waste Production
To learn how to make surfboards, Mike did a 6 month apprenticeship with Nick Aleandro, who has shaped for 20 years under the label “Neto Shapes”. Nick shares our respect for the environment, and our desire to produce surfboards in as efficient a way as possible. He taught Mike methods to minimize wasted resin, re-purpose any trimmings, and minimize our use of disposables.
Add those techniques to the low waste nature of 3D printing, and we don’t need to empty our trash can very often. Even the supports that snap off of our 3D-prints get saved, so we can process them back into filament.
-
Bio-Based Epoxy
Using bio-based epoxy was another easy choice. Our workshop isn’t very well ventilated, and our bio-based epoxy is odorless and has less VOC’s than traditional resins. As an added bonus, bio-based epoxy comes with a much smaller carbon footprint than petroleum-based alternatives. Until we invent a way to make great surfboards without epoxy resin, this is our choice.